Table of Contents
ToggleRCA (Root Cause Analysis) is the process of identifying the underlying causes of problems so that solutions can be developed to prevent a recurrence. Rather than fixing problems, it encourages teams and leaders to work on preventing them instead.
Benefits of Root Cause Analysis
Addressing the root cause of the problem is something that is inherently wired into us in our day-to-day lives, for that matter. But over the years, we’ve been accustomed to treating the evident symptoms rather than treating the root cause of the problem.
The same approach has manifested in our work as well, where we are only looking at the superficial symptoms of a deep-rooted problem that may include resistance to change, culture, inability to embrace newer technology, an overall change in the process structure, and many more.
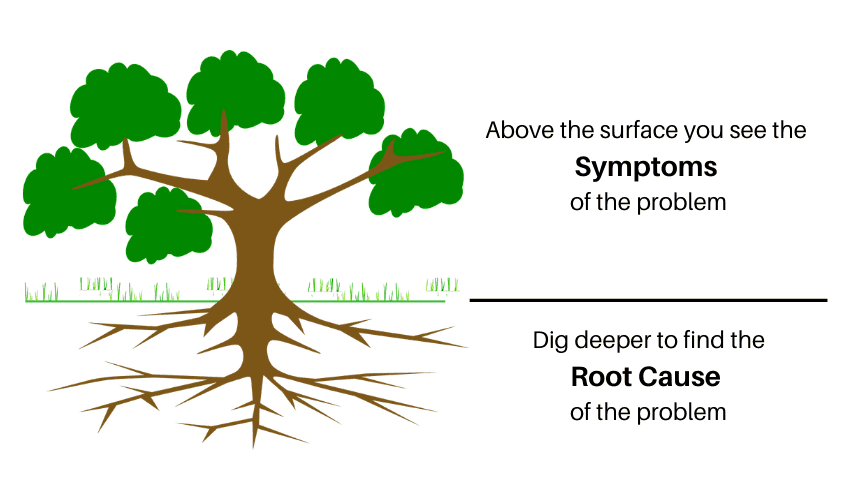
It is here where Root Cause Analysis training helps organizations and professionals belonging to different teams gain a holistic perspective of a problem.
They will dig deeper in terms of problem-solving by using various RCA tools and techniques such as 5 WHYs analysis, Ishikawa Diagram, Pareto Chart, Change Analysis, Control Charts, FMEA, Scatter Plot, and more. Enterprises need to stop firefighting by treating only the symptoms and understanding the underlying issues to fix them permanently.
The RCA can be performed by using various lean tools and techniques, methodologies, and a collection of principles that are inherent to the organization to understand the root causes of an incident or a trend that has been revealing itself over the years in an organization.
This RCA technique can be applied to anything and everything, be it a project, goods, service, new process adoption, or organizational change; it helps us to get to the root of the problem and identify the layers where the problems exist, and address each in a unique way that delivers the best possible result.
Objectives of Root Cause Analysis
There can be multiple objectives for performing root cause analysis in an organization which include:
- First, identify the root cause of the problem, event, incident, or trigger point that led to the change in the order.
- Second, after identifying a root cause, how to fix it, and learning lessons with regard to the underlying issues of a problem
- Third, the application of the lessons learned from the RCA is performed to ensure the problem does not arise again in the future.
Root Cause Analysis Report Examples
The RCA report looks like a simple Word/Excel document that records the events and provides all the necessary details about an incident’s background and contributing factors, root cause, along crucial timeline. The report will also have the details of team members who will be investigating the incident along with methods used to identify it.
Below is a sample RCA report template from Smartsheet that has various other templates as well to conduct Root Cause Analysis thoroughly.
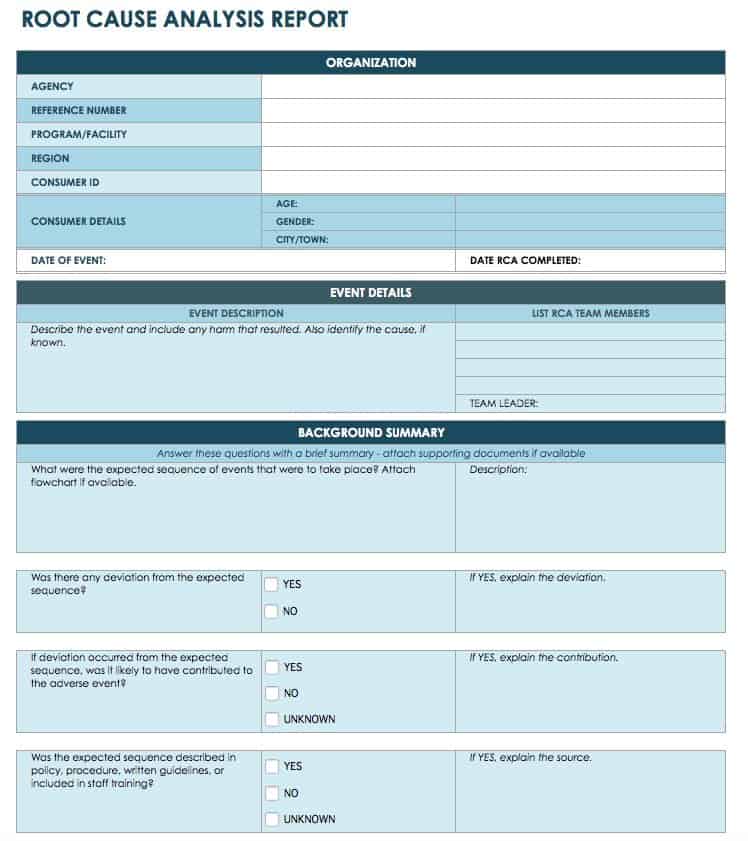
Root Cause Analysis Tools & Techniques
There are various tools and techniques used to perform RCA in an organization, below are some of the most popular ones explained in brief:
5WHYs Analysis
This 5WHY analysis approach is something that is taken based on a toddler perspective approach where children ask questions of WHY until they are satisfied, which provides them with a logical explanation.
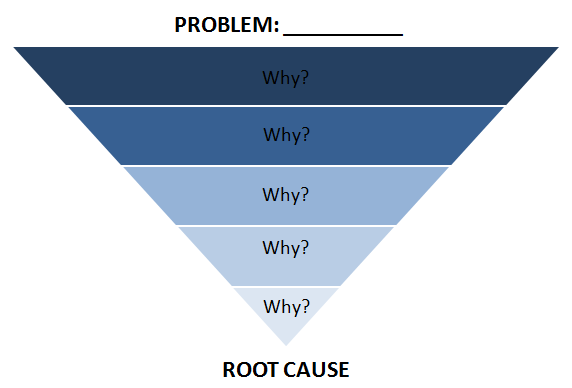
Similarly, when enterprises identify a problem and want to get to the root cause of it, they usually employ the 5 WHYs approach, where one question of WHY will be followed up with another deeper question of WHY. Usually, 5 WHYs are enough to get to the root of the problem, but it may be even as little as two WHYs or as many as 30 WHYs depending upon the underlying issue.
Example of a 5WHY approach
Taiichi Ohno, who is the creator of the 5-WHY technique, introduced it in the Toyota Production System (TPS) to get to the root cause of the problem. Taiichi Ohno asked every individual to observe the production floor without any preconceptions to ask 5 WHYs for every matter/problem.
1. Why did the robot stop?
-> The circuit has overloaded, causing a fuse to blow.
2. Why is the circuit overloaded?
-> There was insufficient lubrication on the bearings, so they locked up.
3. Why was there insufficient lubrication on the bearings?
-> The oil pump on the robot is not circulating sufficient oil.
4. Why is the pump not circulating sufficient oil?
-> The pump intake is clogged with metal shavings.
5. Why is the intake clogged with metal shavings?
-> Because there is no filter on the pump.
Source: Toyota
Fishbone Diagram
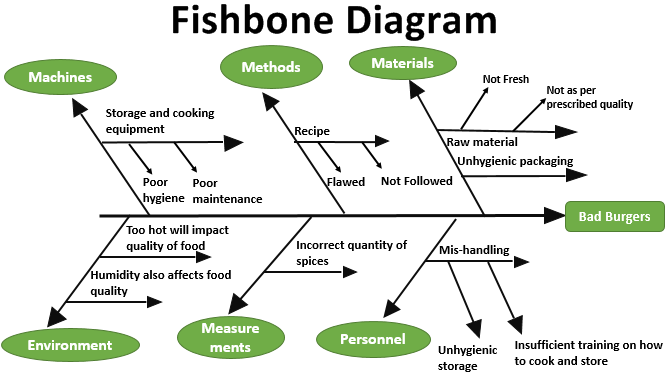
This Fishbone or Ishikawa diagram is another popular RCA technique used by enterprises to find the root cause of a problem. This is in a way similar to the 5 WHY technique but provides better visualization of each cause and its effect to better understand the problem by following the branching of paths and potential causes, which in a way looks like an actual fishbone. The best way to go about this method is to identify broad-level categories where the underlying problem may exist and then draft your causes that have led to the problem, which is in the middle.
Below is a visual representation of a Fishbone Diagram, which will help you clearly understand how enterprises or investigative teams get to the root cause of a problem.
Broad-level Categories to Consider in a Fishbone Diagram:
- Personnel
- Machines
- Materials
- Environment
- Measurement
- Methods
- Management
- Maintenance
- Skills
- Suppliers
- Price
- Marketing
Pareto Chart
Pareto Chart is another popular RCA tool used to analyze various problems and their probable causes. The Pareto Chart is based on a simple 80/20 rule, which means 80% of the problems are only caused due to 20% of the issues. Or one may even look at this as 20% of inputs deliver 80% of results.
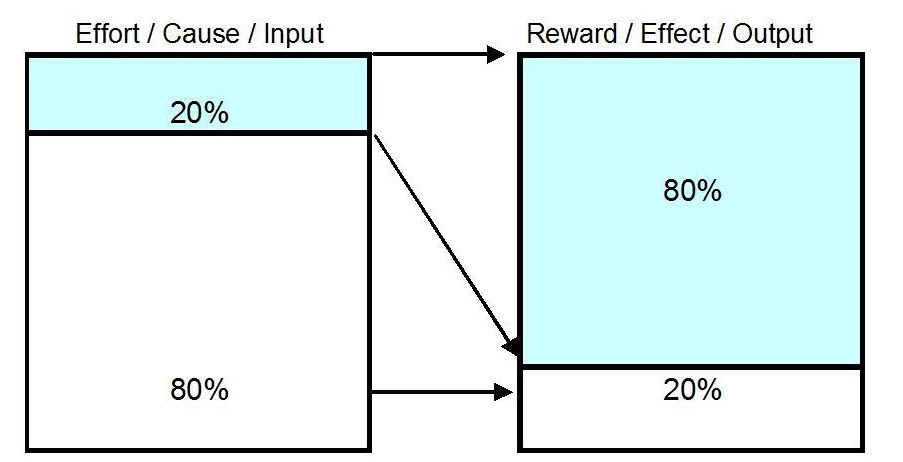
The Ideal Scenario to Use Pareto Chart Analysis
The Pareto Chart analysis can be performed in enterprises across various industry sectors and has the most common function in optimization. Irrespective of the criteria in the form of optimization of code, workflows, documentation practices, and business processes, the Pareto chart can be applied to anything and everything. Through Pareto chart analysis, one can easily find the patterns that can generate the greatest impact by employing critical resources and activities.
Below is a sample Pareto Chart Diagram that shows the audit of types of different medication errors from data collected by the New South Wales Clinical Excellence Commission.
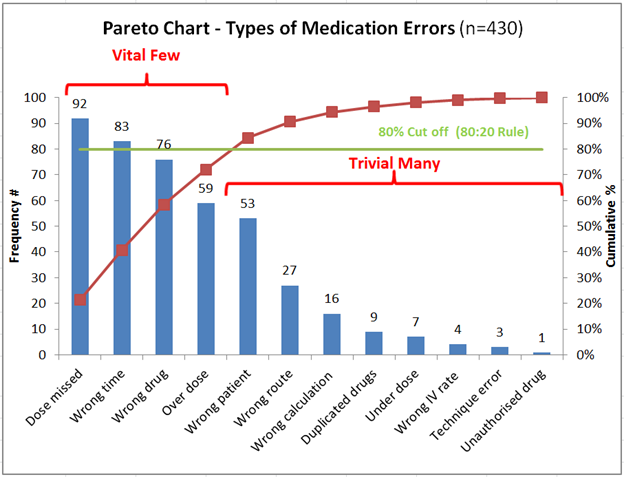
There are other RCA tools and techniques such as Change Analysis, FMEA (Failure Mode and Effects Analysis), Scatter Plot Diagram, and many more used in enterprises across industry sectors worldwide.
For enterprises and professionals to gain a thorough understanding of the benefits of Root Cause Analysis, there are various resources available online in the form of white papers, case studies, articles, videos, and more. But the best way to understand RCA is through undertaking a formal 1-Day / 2-Day RCA training from a recognized training partner like SPOCLEARN. The Root Cause Analysis training course will be delivered by expert Lean Six Sigma practitioners with real-world RCA experience and expertise to analyze data and other critical processes by running them through various tools and performing in-depth investigations.
Industry-wide Adoption of Root Cause Analysis
Many believe Root Cause Analysis is primarily used only in the manufacturing sector, where the quality of the product plays a crucial role in customer satisfaction. But today, the quality aspect is intertwined in anything and everything we do. Customers today are spread across industry sectors through an online medium which has become a bridge between them and businesses. In such a disruptive business environment, it is critical to deliver services/products of the highest quality to ensure your customers are loyal and satisfied every time they interact with you across different mediums.
Major Industries where RCA is used Predominantly are:
- Manufacturing
- Healthcare
- Defense
- Information Technology
- FMCG
- Oil & Gas
- Nuclear Power Plants
In a way, RCA can be used anywhere and everywhere in our day-to-day lives as it is that simple and gives you that logical understanding of any problem that leads to a quick resolution.
How to Implement RCA in an Organization?
The best way to adopt RCA in an organization is to have a holistic understanding of the need and value it will deliver both in the short term and long term. Below are the steps through which an enterprise can quickly adopt RCA:
- The first step is to assign a leader who is well-versed in conducting RCAs for different types of incidents and problems in an organization, or you can bring in an external RCA consultant who has experience in implementing RCA from scratch.
- Devise a team that has a crucial mix of project managers, senior stakeholders, and team leads across departments who are interested in process standardization
- Showcase the benefits of RCA through case study representation, facts, and real-world examples within the organization to educate the team
Create a necessary structure within the organization in the form of an email ID [email protected] for the RCA team members where they record each and every event and incident happening within. - Regularly meet with the team every month once or twice to review the incidents and perform RCA.
- Make the team members really understand the various facets of RCA in the form of Event/Incident -> Root Cause -> Correction -> Corrective Action
- Assigning team members to perform RCA directly gives them more freedom and confidence to identify underlying issues in the organization and to become informed members of the team
Tips for Performe Effective Root Cause Analysis
Below are some of the key tips for effectively performing Root Cause Analysis:
- Ask more questions as this will lead to identifying the real root cause of the problem
- Work with a team, as it is easy for somebody working alone to miss crucial insights right in front of you
- Fine-tune your RCA through practice by being more aware of the process while resolving primary problems, various smaller issues could be resolved all along
- Use RCA for expected/unexpected successes as well to understand what was done right to achieve business objectives
- RCA is all about improving the current system in place rather than penalizing individuals
- Train individuals and enterprise teams in Root Cause Analysis training to help them gain a thorough understanding of RCA tools and techniques and use them in enterprises to identify and mitigate problems.
Root Cause Analysis Training Benefits
The wide range of benefits that enterprises associate with implementing Root Cause Analysis include:
- RCA clearly focuses on the deep-rooted underlying issues/causes and not just mere symptoms that are visible in front of you.
- Helps enterprises to reduce costs and time by catching an issue early and resolving it as quickly as possible.
- RCA helps to resolve real-world problems that businesses face on a regular basis and helps in streamlining processes.
- Root cause analysis knowledge within the workforce helps to make the workplace safer where incidents and events are reported quickly and prevent them from happening again.
- RCA helps businesses to provide long-lasting solutions rather than work on quick fixes.
- Professionals with RCA knowledge are in high demand in enterprises across various industry sectors globally.
- RCA-certified professionals are also highly paid individuals with their salaries ranging anywhere from USD 56,000 to USD 114,000 per annum in the US.
- Effective adoption of RCA saves more than money for the organization. It also helps in the form of upskilling the workforce, which leads to a change in attitude to help businesses continually improve, increase productivity, and even innovate better.
Related Quality Management Training Programs
Root Cause Analysis training is just the tip of the iceberg and can certainly be the start of something unique in your journey towards being exceptional. There are various related Quality Management certification training that open Pandora’s box of knowledge through which businesses and individuals can transform, grow, and stay relevant. Some popular Quality Management certification courses are:
- Lean Six Sigma Yellow Belt
- Lean Six Sigma Green Belt
- Lean Fundamentals
- Quality by Design (QbD)
- Total Quality Management (TQM)
- Quality Function Deployment (QfD)
- Kaizen
- Value Stream Mapping
Conclusion
Root Cause Analysis not only helps individuals and organizations identify the real problems, but it also gives you clarity towards achieving transformation, adopting the mindset of change, embracing a new culture shift, and bringing in better business agility. Leadership plays a major role in giving the go-ahead to adopt newer principles, frameworks, and best practices, and RCA is one such technique that helps organizations to continually improve and remain competitive. Getting the teams trained in the Root Cause Analysis Course is just the beginning of the journey, but the investment will surely yield benefits far beyond anybody’s comprehension.